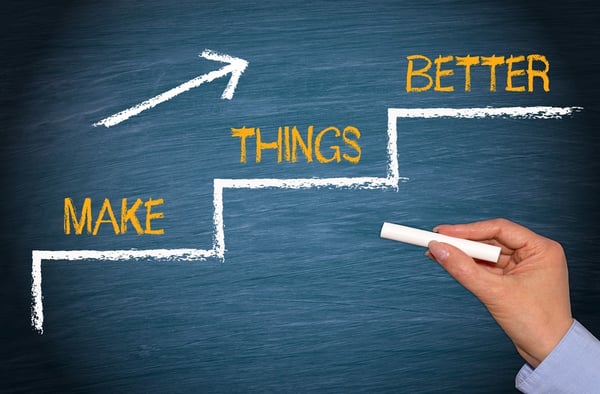
Is Your Company’s Culture Relentless about Improvement?
Continuous improvement
Continuous improvement creates ongoing upgrades in products and services through constant review, measurement, and action. The concept is part of all major quality methodologies, including Six Sigma, Kaizen, and ISO. A basic approach to continuous improvement was pioneered in the late 1930s as a simple cycle of Plan – Do – Check – Act (PDCA).In this approach, you identify a problem and then consider potential causes. Next, you develop a hypothesis and implement a solution on a trial basis. If the hypothesis is validated, you implement the solution. If not, you devise and test alternative solutions until you reach an appropriate resolution. Then the cycle continues with yet another problem to be resolved.
This methodology becomes an unbroken circle, meaning that continuous improvement is a process that never stops.
Author F. John Reh noted,
”The late quality guru W. Edwards Deming said that managers and organizations must have a consistency of purpose and a deep and abiding dedication to constant, ongoing improvement to satisfy customers, beat the competition, and retain jobs. Deming’s focus was on ensuring that continuous improvement was bred into the culture, not something momentary or occasional.”
Deming understood that a system of continuous improvement is not the same as a culture of relentless improvement.
In a culture that is relentless about improvement, employees regularly evaluate their work to find ways to be more effective. They are never satisfied with the status quo. “Because we’ve always done it that way” is not an acceptable answer. Complacency doesn’t exist. The team is laser-focused on finding ways to get things done better, cheaper, faster.
Finding Ways to Do Your Job Better, Cheaper, Faster
A culture of continuous improvement is one of take-charge spirit and empowerment. Once employees are comfortable with the requirements of their role, they should look for ways to do it more effectively. “But that’s the way I learned to do the job” is a starting point. Employees should not be constrained to one approach if they can identify a better, cheaper, faster way to do it. Encourage your team to think creatively about processes.
Cross-developing employees and information sharing across departments can help staff to think differently. Have them ask internal customers what they do with the information they receive. Team members who prepare reports may find that the recipients no longer use the data. They might find more helpful ways to reorganize reports. They may even decide to eliminate them.
Encourage employees to share what they learn while improving processes. Their findings may spark ideas for others. Make sure employees understand that the point is to make everyone more effective. It’s not about personal achievement or out-performing co-workers.
Sometimes the better, cheaper, faster way to perform a process is not to do it at all. Outsourcing may be the preferred long-term answer for the company. Leaders and employees must be open to that possibility.
Embracing Change
Encourage your team to embrace change and growth. Cultures of relentless improvement and welcoming change go hand-in-hand. When processes constantly evolve, your employees cannot get complacent in their roles. Instead, they understand that change is about making the company more effective and competitive.
“Because we’ve always done it that way” is a phrase rooted in emotion and clinging to the comfort of the past. If employees are comfortable with and open to change, they look forward to modifying processes to make them better, faster, and more efficient.
Scheduling a Tune-Up
In our personal lives, we take our cars in for tune-ups to keep from having problems on the road. We get annual check-ups to make sure we’re healthy. At work, we schedule routine maintenance on manufacturing equipment and vehicles to ensure they run optimally and safely. The same principle should apply to how your team approaches their work processes. Regular “check-ups” on your systems, procedures, and practices help to prevent major problems before they happen.
Set regular schedules and goals for process re-evaluation. Scheduled process reviews benefit team members who struggle with developing a continuous improvement mindset. Encourage team members to choose at least one thing each quarter that they want to improve. Then have them develop a plan to achieve that goal and hold them accountable for it. Over time, they’ll incorporate this way of thinking into everything they do.
Developing a Mindset of Improvement
Being relentless about improvement is a mindset. It’s a way of seeing an unlimited opportunity for growth. Encourage your team to be optimistic and open-minded about finding ways to improve everything they do.
Part of developing a continuous improvement mindset is to begin thinking about process improvement as soon as you roll out a new process. Schedule an evaluation and strategy session six months or so out. See whether the process is working as designed, or if it needs to be tweaked to make it more effective. Doing this with a new process teaches employees that you can improve everything, not just methods that have been in place for years.
Schedule a debriefing session after each activity, even something as simple as a sales call. Ask employees to analyze what went well and what they could improve. This exercise helps form a habit of seeking growth opportunities.
Encouraging Employee Buy-In
This mindset of never-ending improvement requires employees to think like an owner of the business. If employees are vested in the business’s success, they will want to do things better, cheaper, faster. Ask your team, “How would you approach this process if this were your company? What might you do differently if you were spending your money?”
As John Reh observed,
“Organizations that excel at continuous improvement incorporate it into their values and reflect it in their hiring and training. They also incorporate it into their employee evaluation and compensation system. Employees take greater ownership in these companies because they are invested in the process of ongoing improvement.”
Align your employee objectives and compensation systems with the relentless improvement goals and mindset you seek.
Developing a Culture of Relentless Improvement
Continuous improvement initiatives will help your organization’s products and services maintain a competitive edge. But the only way to make these initiatives a way of life for your employees is to embed a culture of relentless, unstoppable process improvements.
Company cultures are about behaviors – how people act and do things in your organization. Your company’s leadership should determine and then reinforce desired behaviors.
At CultureWise, one of the behaviors we emphasize with our team is “Be relentless about improvement.” We explain this behavior as:
Regularly reevaluate every aspect of your job to find ways to improve. Don’t be satisfied with the status quo. “Because we’ve always done it that way” is not a reason. Keep getting better.
CultureWise CEO and author David J. Friedman developed the CultureWise system to help business leaders identify, define, and promote behaviors that result in strong company cultures. The approach is outlined in Friedman’s book Culture by Design.
Want to learn more? The CultureWise website is full of resources on company culture and implementation. Explore the website, and then connect with one of our representatives to learn how CultureWise can jumpstart your company’s culture. And be sure to sign up for a complimentary subscription to our newsletter, Culture Matters.