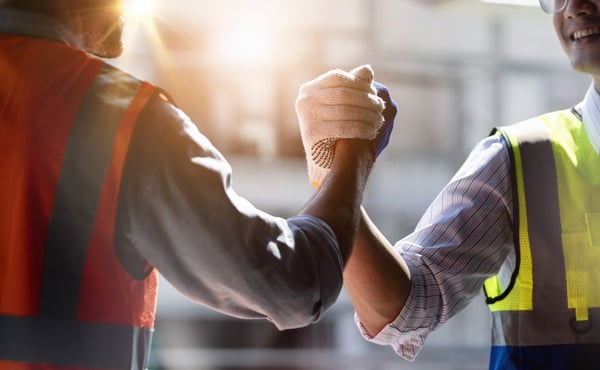
How to Develop a Safety Culture and Prevent Occupational Hazards
Safety is crucial to many industries, such as those that involve heavy machinery, complex equipment, chemicals, and health procedures. Unfortunately, accidents and adverse events often plague companies that regularly grapple with workplace hazards. But leaders can protect their workers and continuously minimize risks on the job by cultivating a safety culture.
What Is a Safety Culture?
In Occupational Health and Safety (OHS), Peter Furst described “safety culture” as the “truths, ideas, and beliefs that all members of the organization share about risk, accidents, injuries, and occupational health.” It is an environment where everyone’s behaviors and attitudes reflect that health and safety are paramount.
But it’s difficult to establish a safety-first environment without a dynamic company culture to support it. As Scott Gaddis wrote in OHS:
“Safety culture is, in all reality, a subculture of organizational culture. It's simply a granular focus in one part of the overall management system and can be stalled or elevated by corporate culture.”
Gaddis notes that to build a safety culture, the first question corporate leaders should ask is:
“Do we have the right organizational culture that reflects how we want to protect our people, and if not, how can we improve?”
This kind of introspective assessment will help leaders understand which behaviors should be taught and reinforced to create a culture that prioritizes safety.
5 Things That Undermine Safety Culture
Most companies dealing with workplace hazards have protocols to reduce injuries and incidents. But having safety rules and complying with them are not the same thing.
The authors of a McKinsey article suggest that the reason behind the disconnect is that organizations pay too much attention to the tools and processes for safety without considering five employee mindsets that can limit their success:
- Fear of blame
- Disempowerment
- Fear of productivity loss
- Fatalism
- Complacency
FEAR OF BLAME
In a culture where managers are quick to blame and point to mistakes, people are less likely to report safety issues for fear of punishment. For example, the National Employment Law Project found that 43 percent of low-wage workers in three major U.S. cities experienced retaliation after filing a safety-related complaint.
Major safety breakdowns will usually come to light. But workers often sweep minor incidents under the rug to avoid unpleasant fallout. While they might not be life-threatening, everyone misses an opportunity to learn when these situations aren’t reported, which degrades safety even further.
DISEMPOWERMENT
Often safety regulations fall short because leadership doesn’t seek input from the people performing the hazardous work. As a result, sometimes what seems reasonable on paper isn’t practical in the field, and a “safety is someone else's responsibility” cycle ensues.
For example, leaders will say that injuries would decrease if employees just followed the rules, and frustrated workers bend the rules because they don’t always make sense. Incidents decline when the two groups communicate and work together to manage safety.
FEAR OF PRODUCTIVITY LOSS
Companies pay their employees to deliver results, which can often seem antithetical to following multi-step safety protocols. Unless management clarifies that safety is the top priority, workers may try to cut corners to meet deliverables. And when team members watch their coworkers doing this, they’re more likely to follow suit.
However, skirting safety processes results in more accidents and lower morale and ultimately disrupts productivity. Ironically, according to a recent study in Occupational Health Science, “employees’ safety and health are key elements in achieving an organization’s desired productivity and efficiency.”
FATALISM
The elephant in many workplaces is the belief that injuries are just part of the job. In these environments, people sustaining minor injuries don’t report them because they consider them normal. This tolerance stems from the notion that some risks can’t be avoided—even in organizations where managers pledge to achieve “zero safety incidents.”
The key is for leadership and employees to get in sync with this aspiration. Instead of just setting policy, leaders should create stretch but achievable targets for reducing injuries. People are more likely to commit to the goal when safety is placed in the proper context.
COMPLACENCY
When safety issues are frequent, many managers feel overwhelmed and resign themselves to a slow improvement pace. Even those committed to solving the problems fear it would take years to implement a culture shift, and worry that initiating the change would be a hassle.
Too often, managers don’t act until they have to deal with the aftermath of a serious accident. But, as the McKinsey authors point out: “A failure to enlist key influencers, generate momentum, and deliver the early wins is critical for successful transformation.”
4 Ways to Build & Strengthen a Safety Culture
After identifying the mindsets hindering a safety culture, leaders must help team members change their perspectives. The McKinsey article authors identify four methods to create a safer workplace.
1. Reward safe behaviors.
Companies often zero in on the negative outcomes of accidents, so the concept of safety keeps employees on edge. But unfortunately, many organizations don’t react to the absence of incidents or when protocols are followed.
Leaders can change that dynamic by not only helping their team learn from accidents but also by creating a system of meaningful acknowledgment to celebrate successes. For example, they could recognize employees who consistently follow the rules, notice and prevent problems, and work together to prevent accidents.
2. Clarify that safety is the priority.
Employees can’t effectively perform unless management sets clear expectations. For example, they’re more likely to make unsound decisions if they receive mixed messages about safety and productivity. To prevent accidents, leaders must clearly communicate that safety is paramount, even if the accompanying rules slow the work pace.
Leaders should do more than issue target goals. Instead, they should develop reasonable production timelines and stress to employees that following safety procedures is part of the process.
3. Develop soft skills.
Beyond the technical aptitude to perform their job, people also need the soft skills that will enable them to succeed in their roles. For example, to build a successful safety culture, leaders should help team members develop capabilities like building self-awareness, speaking up and asking thoughtful questions, sharing information, and collaborating.
Managers should coach their people to tune into their surroundings and also make them feel comfortable to speak freely about issues. Employees should be empowered to identify hazards and control risk and encouraged to contribute to a positive and caring team environment.
4. Model behaviors from the top.
Employees take their cues from their leaders and look to them to set the tone in the workplace. For example, if their boss doesn’t make safety procedures a priority, workers will follow their example.
Leaders have a responsibility to model and support the behaviors that create a safe workplace. They can demonstrate their commitment to this initiative by walking the talk regarding safety measures. And they should also reinforce safety’s importance by regularly addressing it in meetings, informal discussions, and internal communications.
Benefits of a Safety Culture
Leaders who develop a positive and proactive safety culture protect their staff and also strengthen their companies in five significant ways.
- Higher employee engagement
Workers operating in a safety culture are more satisfied and vested in their jobs than those who don’t have the same assurances. Higher employee engagement creates stronger trust and relationships between management and team members. - Improved productivity
Employees who feel safe at work are more motivated to perform at a high level. Additionally, consistent safety standards and procedures help team members work more efficiently, boosting productivity. - Fewer legal concerns
Having a safety culture allows companies to better comply with industry standards and regulations, reducing legal entanglements. - A well-educated team
A safety culture promotes learning and helps educate all levels of staff. Highly informed employees take fewer unnecessary risks and make better decisions. - Better reputation
The public applauds companies that demonstrate care and respect for their employees. A safety culture helps organizations build a positive image, resulting in more customers, profit, and top job candidates.
An effective safety culture also promotes accountability and a team-first atmosphere. Instead of worrying about covering their mistakes, employees look ahead and anticipate issues and prevent them before they happen. When errors occur, they focus on solutions instead of blame. And because a safety culture galvanizes teams, workers are more likely to look out for one another.
As noted earlier, the positive behaviors that form a safety culture must be rooted in the broader organizational culture. Leaders can create that infrastructure by identifying, defining, and promoting the behaviors that will generate organizational success.